Rozwiązania technologiczne
Wytrawianie i pasywacja w czystych i bezpiecznych warunkach.
Opierając się na ponad 70 lat doświadczeniach w badaniu, projektowaniu i produkcji urządzeń, kolejną innowacją firmy Delmet stał się komorowy system do wytrawiania stali. Instalacje natryskowe działające w podobny sposób, jak przez wielu z nas używane zmywarki do naczyń, spowodował optymalizację zużycia preparatów chemicznych, kosztów produkcji poprzez ograniczone zużycie wody i energii.
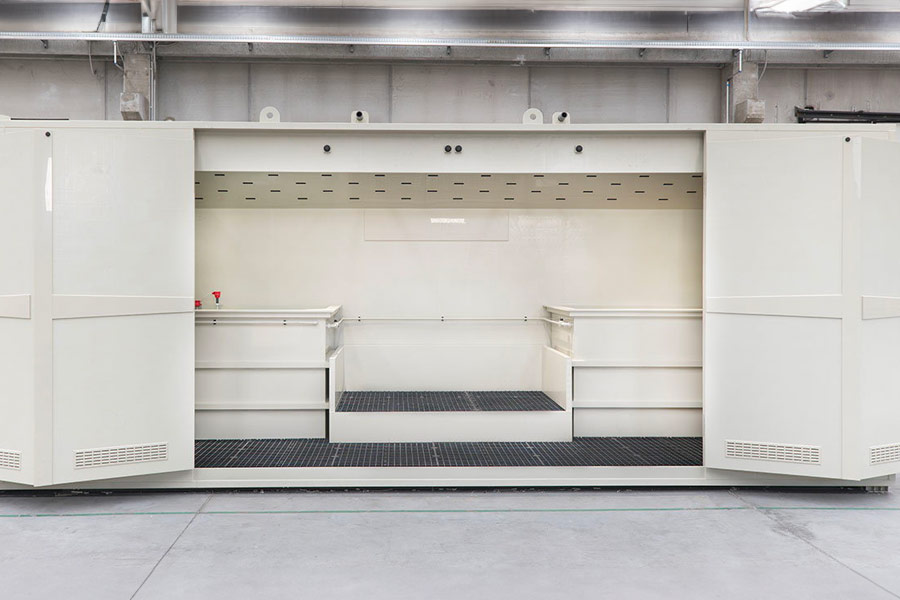
Posejdon - komorowy sytem do wytrawiania stali
Posejdon, bo o nim mowa to koncepcja komorowego sytemu do wytrawiania stali, która opiera się na pracy środkami chemicznymi w obiegu zamkniętym odizolowanym od otoczenia, z wyeliminowaniem udziału pracownika w czasie ścisłej obróbki chemicznej. Jest instalacją innowacyjną i zaawansowaną elektronicznie, która posiada panel oprogramowania wraz z remote control. Poza tym instalacja ta spełnia wszystkie wymagania Przemysłu 4.0 i może być połączona z serwerem w celu monitorowania wszystkich parametrów zużycia wody, energii elektrycznej i produktów chemicznych.
Komorowy system do wytrawiania stali posiada wewnętrzny system wentylacyjny, który uaktywnia się jedynie podczas pracy, a system ogrzewania jest szybki i energooszczędny. Brak przy tym toksycznych oparów chemicznych i przykrych zapachów w hali podczas pracy. Nie ma konieczności czasochłonnych szkoleń lub szukania pracowników z doświadczeniem przy obróbce chemicznej stali.
Posejdon gwarantuje bardzo niskie zużycie preparatów chemicznych. Standardowe wytrawianie stali metodą natryskową powoduje jednokrotne użycie preparatu wytrawiającego. Metoda zanurzeniowa (kąpielowa) to konieczność zalania jej odpowiednią ilością preparatu wytrawiającego. Dla przykładu wanna o wymiarach 4 x 2 x 1 m (standardowe wymiary wanien trawiących) potrzebuje około 7,5 m3 kąpieli. Jeżeli cykl produkcyjny przewiduje 3 procesy, np. odtłuszczanie, wytrawianie i pasywację oznacza to, że potrzebujemy 3 wanny i około 22 m3 różnych preparatów chemicznych.
Komorowy system do wytrawiania stali przy realizacji trzech cyklów obróbki, potrzebuje około 250 litrów chemii wielokrotnego użytku na jeden proces. Ubytki preparatów chemicznych są uzupełniane automatycznie. Aby zoptymalizować rezultat obróbki i zmniejszyć zużycie wody wraz z komorowym systemem do wytrawiania stali można dostarczyć instalacje do oczyszczania i regeneracji wody, która dodatkowo zwiększy oszczędność jej zużycia do 70%.